Which Standalone ECU is Right for You?
So, you’ve decided that using a standalone ECU is going to be the right choice for your particular project. Naturally, the next question then becomes, which one? As with many parts of our project cars, the answer becomes easier when we have clearly defined goals in mind from the beginning. That is not to say that projects can’t change direction mid-build or a rule change might come about, creating an opportunity, but having a good idea of where we need to end up right from the start is going to make things smoother all along the way.
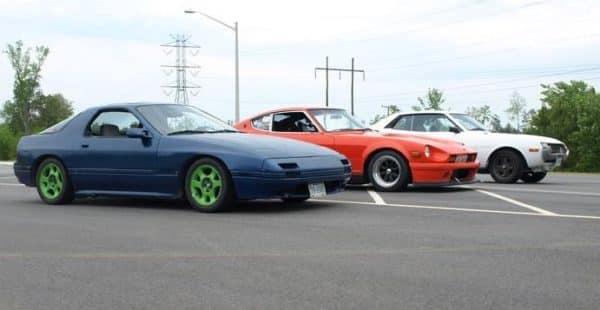
In this week’s article, I’ll be using some of my own experience working as a part of the DIYAutoTune.com technical support team along with personally setting up standalone engine management systems on several vastly different types of vehicles. By far, the most frequently asked question I remember seeing fill my inbox every day was some form of: “Which system should I use to run engine “X” in chassis “Y” with these particular modifications?” Let’s jump in to help take the mystery out of those fancy black boxes, and make the right choice to fit your application, end goals, and budget.
MSPNP the Standalone Easy Button
Before we jump into the various standalone ECU options best suited for your application, we need to talk about the powerful MSPNP or “Plug and Play” offerings. Imagine going from your stock engine control module to a full-function programmable standalone ECU in less than an hour! MSPNP makes this a reality. These systems are powered by the same processing power and take advantage of the same tuning interface as all the other MeqaSquirt products, but come packaged in a unit that directly replaces your factory engine management computer, plugging into your existing wiring harness.
This opens the door to modifications the original equipment computer could never handle, like boost control, launch strategies, nitrous control, closed loop AFR, engine safeties, and a host of others. Another advantage that sometimes gets overlooked is the option to ditch the factory airflow meter or MAF on equipped vehicles. This not only can free up some flow by taking the MAF restriction out of the intake but eliminates the limitations inherent in the MAF sensor itself. On top of all that, these units are pre-loaded with startup maps with all the fuel and ignition settings pre-made, taking the guesswork out of the equation and getting you up and running in the quickest way possible. See if there is an MSPNP option for your combination and start tuning today!
Fuel and Spark
There are a handful of decisions we’re going to need to make upfront before pulling the trigger on a particular ECU. One of the first is: are we controlling fuel only, or fuel and ignition? While many ECUs have a lot of other functionality, what we need first and foremost to get our project up and making noise is fuel and spark. Right out of the gate let’s talk about fuel injectors, specifically the type and number of injectors we plan to use. Are we using 1 single injector at the throttle body, 4 injectors batch fired in their stock location, or 8 sequentially fired high-flow units? This is important because we are going to want to match our ECU’s injector driver capabilities to our project needs.
Standalone units such as the MS2 and MS3 base ECUs come equipped with two injector drivers. While the MS3X and MS3Pro-based units can have as many as 10 individual injector outputs, the MS3Pro EVO unit delivers the capability of up to 12 sequential fuel injector outputs. Does this mean we can only use 2 injectors if we only have 2 injector drivers? Absolutely not. The beauty of using a batch-fired injection strategy means that we can wire our injectors in a way that fires them in “banks” or “batches”. Using this strategy we can fire 4 injectors with each driver in a V8 configuration, 2 per output in a 4 cylinder, or 3 per driver with a 6 banger.
For a deeper dive into the merits of batch vs. sequential injection strategies, Mr. Greg Banish has done an excellent job of comparing the two in his article: Sequential vs. Batch Injection Timing. What we hope to accomplish here is arming you with the information needed to make the right choice for your particular project. While there are no doubt benefits to the added precision of a sequential fuel injection strategy, there are many cases where it just may not be a necessity.
Injector Impedance: High or Low?
What we need to discuss next are two different types of fuel injectors we are most likely to encounter. Low Impedance or High Impedance. Without getting too far into the weeds here, which will come later, the important thing to remember is that injector impedance or resistance is critical in the ECUs injector driving strategy. Low-impedance injectors, just as the name implies have a lower internal resistance in the coil of the injector itself. You can find this out by using an ohmmeter across the two terminals in the injector and measuring resistance. 2.5 to 4.0 ohms is considered low impedance. While high-impedance injectors would be in the 12 to 16 ohm range. The design of the injector has a direct effect on the electrical current needed to operate, and the ECUs internal strategy for opening the injector.
Low resistance injectors are generally found with extremely high flow rates, where faster response times are more critical. High-impedance injectors are far and away the most common type found installed from the factory. The low current draw keeps the heat down while allowing multiple injectors to be controlled with one driver. This in turn can simplify wiring and keep costs in check. Fortunately for us, standalone engine management will allow us to run either style. While there are advantages to each type it is critical to know which style you plan to use.
Ignition Systems and RPM Inputs
What style of ignition system will you be using, and what will you be using for engine position/RPM? These are two very important questions we’ll need to answer before jumping into which engine management system is going to be right for us. Will your project use the stock single coil and distributor like a GM HEI, a wasted spark distributorless setup with a coil pack like the IGN-6, or a direct coil on plug ignition like IGN1A smart coils? The number and style of ignition outputs needed from the ECU will play a major role in deciding which unit is going to be right for you.
What we’ll also need to take into consideration will be the number and style of engine position inputs. It doesn’t matter how well your engine is built or how perfectly your wiring is run, nothing is getting done by the ECU until it knows the engine RPM. This can be as simple as supplying an RPM input from the tach signal on a single coil distributor system, a toothed wheel crank trigger setup, or as complex as factory-style cam/crank position sensors used for sequential control. Making the call on what type of ignition system and RPM input you’ll be using can save you and your tuner major headaches down the road.
MegaSquirt-II, The DIY Solution
By far, one of the most economical ways to get into a standalone engine management solution for your vehicle is the MegaSquirt-II or MS-2 available in a build-it-yourself kit or pre-assembled from DIYAutoTune.com. Don’t let the entry-level pricing fool you, this is an extremely capable unit, with the ability to run nearly any engine combination when properly configured. The basic inputs required for any standalone engine management are all there along with some great extras. Some of the major considerations are:
- Cam/Crank input options: The MegaSquirt-2 engine management is capable of reading nearly any VR (variable reluctance), Hall Effect, Optical, or coil negative RPM input you can imagine along with a large number of O.E.M. style toothed wheel patterns. However, each of these can require different changes inside the MegaSquirt unit itself. Fortunately, the documentation found at msextra.com is comprehensive and covers every combination in detail.
- Ignition Outputs: One of the things that makes the MegaSquirt-2 so powerful, and economical is the ability to make modifications to the ECU board as needed. Right out of the box, the MS-2 is well suited for fuel-only installations, or installs where only 1 coil with a distributor is used. With modification though, it can be used to run nearly anything you could want.
- Injector Outputs: There are two injector outputs on the MS-2 ECU. The easiest and most common use would be in a “batch” fired configuration, using one driver for one “bank” or set of injectors and one driver for another. This does not allow for a full sequential injector strategy but is acceptable for a wide range of installations. Especially when using the MegaSquirt in place of a factory ECU on a vehicle that was fuel injected from the factory as most early EFI systems were designed this way from the start.
MegaSquirt-3 and MS3X, The Next Level in Tuning Potential
Need something a bit more capable, while still keeping the DIY spirit alive? Or do you require more I/O availability in a pre-assembled unit while keeping the budget in check? Then the MS3 line could be the answer for you. While still providing the flexibility to install on nearly any engine in nearly any chassis, the MS3 and MS3X line has all the features typically found in standalone ECUs costing nearly twice as much. While we are not going to go over every feature of the MS3 in this article, here are some features that might help narrow down your decision.
- Injector Options: The MegaSquirt 3 ECU with the MS3X expansion option opens a world of possibilities for injector arrangements. Whether you need to run 8 individual injectors sequentially or a V12 using a wasted spark strategy and batch fire injection the MS3 can support your combination. By making use of up to 8 high current injector drivers the possibilities truly are wide open.
- Ignition Outputs: When used with the MS3X expansion you will have at your disposal up to 8 logic level ignition outputs. This opens up the world of individual coil-on plug conversions when using “smart” style coils as well the possibility to use any number of high current coil options when paired with an external ignitor module.
- Expanded I/O Capability: As mentioned before, one of the biggest advantages of ECUs in this class is expanded configurable inputs and outputs. Want to have a button to switch between fuel maps? How about arming a nitrous oxide system? Or, What if we wanted to use an electronic boost controller to really turn up the power while maintaining total control? These are just a few examples of how expanded I/O can really take your project to the next level. Combine all of these with onboard SD card data logging, and CANBus communication capability and you have an extremely powerful solution.
Time to go Pro: MS3Pro Ultimate and MS3Pro EVO
So, it’s time to get serious. Then the MS3Pro family of ECUs is what you’ve been looking for. With the ability to run up to 10 injectors sequentially and more I/O than you could imagine, this ECU gives you the power to take total control of almost anything! Designed to be robust and compact while packing a powerful punch the MS3Pro Ultimate is at the top of the standalone engine management game. With over 50 different ignition modes supported, from the ever-present LS family of engines, Chrysler Hemis, and Ford’s Coyote line it truly is easier now to take advantage of these modern powerplants. K-series Hondas, Nissans, Subarus, I think it’s fair to say that no other engine management system anywhere supports this many different engines out of the box. Pour on the boost with turbocharging or supercharging and take it to another level, while giving you complete control over boost, fuel, and timing tables.
- All of the fuel and ignition control: As mentioned, there are very few injector or ignition combinations the MS3Pro family of ECUs isn’t capable of controlling. In extremely high horsepower applications the ability to use any injector on the market means you’ll always be able to fuel the fire.
- Data, Data, and More Data: It takes more to get from the starting stripe to the finish beams than making big power. We need data, and we need a lot of it. Not only do we have enormous data logging power with up to 64 channels logged internally, but CANBus communication capability means we can talk seamlessly to our race dashes to display that data to the driver.
- Take advantage of the latest tech: It’s no secret that technology has made leaps and bounds in terms of engine management recently. One of the most interesting areas of that has been with VVT or Variable Valve Timing control. Being able to monitor and change cam timing on the fly under any conditions can be a game changer. Not only does this open up the possibilities for installation on platforms originally VVT equipped, but opens up the floodgates for engine swap possibilities into our older chassis. Another technology we can take advantage of is the use of a FlexFuel sensor. This device actively measures the alcohol content when using ethanol-based fuels, allowing for boost, timing, and fueling to be optimized at all times no matter what. This can be extremely useful when using fuels of unknown alcohol content while still maintaining the maximum power output possible.